How to Choose an Enterprise App Firm in Canada: A Comprehensive Guide
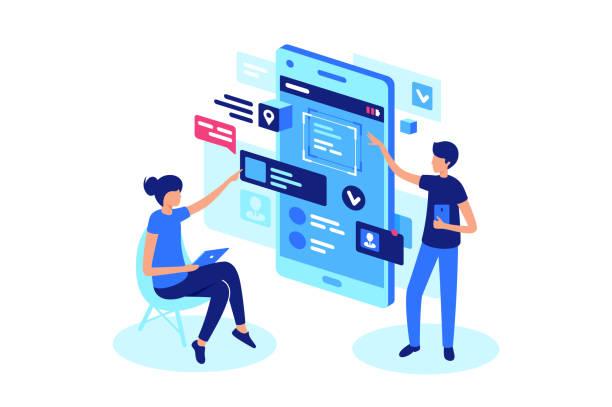
When it comes to building robust and scalable enterprise applications, choosing the right mobile app development company in Canada is paramount. Enterprise apps are critical to streamlining business operations, improving productivity, and enhancing customer experiences. However, selecting the best mobile application development firm to partner with can be challenging, considering the multitude of options available.
In this guide, we’ll walk you through the key factors to consider when choosing an enterprise app firm in Canada, focusing on finding the right fit for your specific needs. From evaluating technical expertise to understanding pricing models, we’ll help you navigate the decision-making process. Along the way, we’ll highlight Devherds as one of the top mobile app development companies in Canada.
Understanding the Importance of Enterprise App Development
Before diving into the selection process, it's important to understand why enterprise app development is essential for your business. Enterprise applications are large-scale, customizable software solutions designed to meet the unique needs of a business or organization. These apps streamline internal processes, improve collaboration, and can even provide a competitive edge by enabling automation, real-time data analytics, and better decision-making.
To achieve all of this, you need a skilled and experienced team of mobile app developers in Canada who understand the complexities of enterprise-level solutions. Whether you need a customer-facing app, an internal tool for employees, or a system for managing operations, partnering with a reliable development firm can make all the difference.
What to Look for When Choosing a Mobile App Development Company in Canada
1. Industry Experience and Specialization
One of the first factors to consider when selecting a mobile app development company in Canada is their industry experience and specialization. You’ll want a firm that has a proven track record of working on enterprise-level applications, as these projects require advanced technical knowledge and the ability to scale.
2. Portfolio and Case Studies
A strong portfolio and well-documented case studies are indicative of a company's capabilities. Look for a top mobile app development company in Canada that showcases a diverse range of successful projects, particularly in the enterprise sector. The more relevant the portfolio to your needs, the better.
Reviewing case studies allows you to gain insight into the company's approach to problem-solving, user experience (UX) design, and the overall functionality of their apps. Make sure to ask for examples of both small and large-scale projects to ensure they have the experience to handle your requirements.
3. Expertise in Latest Technologies
Enterprise mobile application development in Canada demands proficiency in the latest technologies, frameworks, and tools. Your development partner should be adept in popular platforms such as iOS and Android, as well as emerging technologies like cross-platform development, cloud computing, and artificial intelligence.
If you’re considering a mobile application development company in Canada, make sure they stay updated with industry trends and can offer modern, future-proof solutions.
4. Client Reviews and Testimonials
Client feedback is an excellent way to gauge the reliability and professionalism of a mobile app development services provider in Canada. Look for reviews on platforms like Clutch, Google, and other business directories. Don’t hesitate to ask the company for references or testimonials from previous clients.
A reliable app development firm should have a history of delivering quality products on time and within budget.
5. Scalability and Flexibility
As your business grows, so too will your app’s requirements. It’s essential to choose a development company that understands scalability. The best mobile app developers in Canada can create applications that can easily scale as your business expands.
Ask the development firm about their approach to future updates, maintenance, and integration with other systems. Scalability isn’t just about handling more users; it also involves adding features and improving performance over time.
6. Transparency and Communication
Clear communication is critical when collaborating with a development team. Your chosen mobile app development company in Canada should provide regular updates, be open to feedback, and ensure you’re involved throughout the process.
Transparent communication not only builds trust but also helps avoid misunderstandings and potential delays. Make sure they use project management tools that allow you to track progress easily.
7. Development and Deployment Process
Understanding the firm’s development process is essential for managing expectations. Do they follow an Agile methodology or a more traditional Waterfall approach? An Agile development model is often preferred for mobile app development, as it allows for flexibility and iterative improvements.
Moreover, find out about their testing process. A solid testing strategy ensures that the app will be free from bugs and perform well under various conditions.
8. Post-Launch Support and Maintenance
App development doesn’t end when the app is launched. Ongoing support and maintenance are critical to keeping your application running smoothly. Check if the mobile app development services in Canada include post-launch support, bug fixes, and regular updates.
A reliable mobile app development company in Canada will have a long-term support plan in place to ensure the success of your app over time.
Why Choose Devherds for Your Enterprise App Development Needs?
Among the myriad of options available, Devherds stands out as a top choice when searching for the best mobile app development company in Canada. With a strong track record of delivering high-quality, scalable, and user-friendly enterprise applications, Devherds has earned a reputation as a leading mobile application development company in Canada.
Here’s why Devherds is the best partner for your enterprise app development:
1. Proven Expertise in Enterprise Solutions
Devherds specializes in developing custom enterprise mobile applications that solve complex business challenges. Whether you need a CRM solution, an ERP system, or a custom tool for your team, Devherds has the expertise to design and implement powerful applications tailored to your unique needs.
2. A Team of Experienced Mobile App Developers
The company boasts a highly skilled team of mobile app developers in Canada who have extensive experience working with businesses of all sizes. Their expertise covers iOS, Android, cross-platform development, and much more. This versatility ensures that Devherds can build solutions that are both innovative and reliable.
3. End-to-End Development Process
Devherds follows a comprehensive, end-to-end approach to mobile app development. From ideation and UI/UX design to coding, testing, and deployment, they handle every aspect of the development process. This ensures a seamless experience for clients and a high-quality final product.
4. Customer-Centric Approach
Devherds places a strong emphasis on understanding the client’s needs and objectives. They believe in creating long-term partnerships and work closely with clients to ensure their enterprise app aligns perfectly with their business goals. This personalized approach has earned them a reputation as one of the top mobile app development companies in Canada.
5. Agile Development Methodology
Devherds employs Agile methodologies, enabling them to deliver apps faster and make adjustments based on client feedback. This iterative approach ensures that the final product is exactly what you envisioned, with regular milestones and updates along the way.
6. Post-Launch Maintenance and Support
After launching the app, Devherds doesn’t just walk away. They offer robust post-launch support and maintenance services to ensure your app continues to perform optimally. Whether it’s updating the app for new operating system versions or adding new features, their team is always ready to help.
7. Proven Track Record
Devherds has worked with a wide range of clients across different industries, from healthcare to finance to e-commerce. Their portfolio reflects their ability to create scalable and high-performance enterprise mobile apps that meet the specific needs of their clients.
Final Thoughts: Making the Right Choice
Choosing the right mobile app development company in Canada can significantly impact the success of your enterprise application. By carefully considering factors like industry expertise, development process, scalability, and post-launch support, you can find a partner who will deliver a solution that fits your needs.
When it comes to exceptional mobile app development services, Devherds stands out as a top choice. Their experienced team, customer-centric approach, and comprehensive service offerings make them one of the best mobile app development companies in Canada. Whether you’re looking to build a simple mobile app or a complex enterprise solution, Devherds has the skills and experience to bring your vision to life.
Don't settle for anything less than the best. Partner with Devherds, and take your enterprise app to the next level today!