Top Features to Look for in Beer Inventory Software
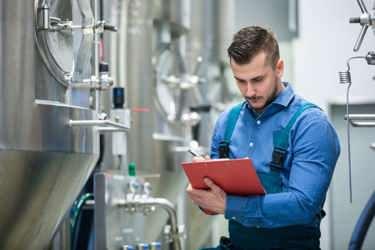
Running a brewery requires more than just crafting great beer—it also demands precision, organization, and efficiency. With the complexities of batch tracking, keg returns, compliance, and distribution, managing inventory manually can quickly lead to chaos. That’s where beer inventory software steps in. Tailored to the brewing industry, this software helps streamline operations, reduce waste, and improve traceability. In this article, we’ll explore the top features to look for in beer inventory software to help you choose the right solution for your brewery in 2025 and beyond.
1. Batch and Lot Tracking
One of the most critical features for breweries is the ability to track batches and lots from production to sale. Good beer inventory software should:
-
Assign unique identifiers to each brew batch
-
Track ingredients and additives used in each lot
-
Record dates for brewing, bottling, and kegging
-
Provide full traceability for recalls or quality assurance
This feature ensures compliance with safety regulations and improves quality control across your production process.
2. Keg and Container Management
Whether you’re managing hundreds or thousands of kegs, knowing their location and status is essential. The software should allow you to:
-
Track keg assignments, returns, and rotations
-
Monitor keg aging and cleaning schedules
-
Record container deposits and credits for each customer
Effective keg management reduces loss, improves turnaround, and increases profitability.
3. Real-Time Inventory Tracking
In a fast-paced brewing operation, you need up-to-date information at your fingertips. Look for software that:
-
Tracks raw materials, finished goods, and packaging supplies
-
Provides real-time stock updates across multiple locations
-
Supports barcode or QR code scanning for easy input
Real-time visibility prevents overproduction, stockouts, and waste, helping your brewery run more smoothly.
4. Production Planning and Scheduling
Beer inventory software should integrate production planning to help you manage:
-
Brewing schedules and tank assignments
-
Ingredient availability and reordering thresholds
-
Batch yields and anticipated outputs
This planning capability helps align production with demand, reduce downtime, and minimize ingredient shortages.
5. Sales and Distribution Integration
For breweries selling directly to retailers, bars, or taprooms, it's vital to have integrated order management. Top-tier software should:
-
Sync sales orders with available inventory
-
Track shipments, deliveries, and returns
-
Support multi-channel sales, including taproom POS, wholesale, and online orders
Sales integration ensures accuracy and transparency across the sales cycle, improving customer satisfaction and operational efficiency.
6. Regulatory Compliance and Reporting
Breweries must adhere to strict reporting requirements, including TTB (Alcohol and Tobacco Tax and Trade Bureau) compliance in the U.S. Your software should offer:
-
Automated TTB and excise tax report generation
-
Ingredient traceability and documentation
-
Audit trails for inspections and certifications
Compliance features save time, reduce legal risk, and ensure you're always ready for inspections.
7. Recipe and Formulation Management
The heart of your product is your recipe. Choose software that allows you to:
-
Store and version brewing formulas
-
Link recipes to ingredient inventory
-
Adjust recipes based on batch sizes or availability
This ensures consistency in flavor and quality across every batch, while also helping with cost tracking and planning.
8. Multi-Location and Warehouse Support
As your brewery grows, so do your storage needs. The best inventory systems can handle:
-
Multiple storage facilities and taprooms
-
Real-time transfers between locations
-
Location-specific inventory tracking and reporting
This allows for centralized control of distributed inventory, keeping operations efficient and organized.
9. Mobile Access and Cloud Support
Modern brewers need flexibility. Look for a cloud-based solution that includes:
-
Mobile access for on-the-go inventory checks
-
Remote updating and monitoring of stock levels
-
Secure cloud backups and automatic updates
Mobile access improves collaboration and decision-making across your team.
10. Robust Analytics and Reporting Tools
To grow your business, you need data-driven insights. Quality software should include:
-
Inventory turnover and cost analysis
-
Sales trends by product, season, or region
-
Customizable dashboards and reports
These insights help you optimize production, reduce costs, and maximize profits.
Conclusion
Selecting the right beer inventory software isn’t just about keeping track of kegs and ingredients—it’s about transforming how your brewery operates. With features like batch tracking, real-time inventory, sales integration, compliance support, and advanced analytics, the right system can improve efficiency, reduce waste, and fuel growth.