Understanding the Slurry Pot: A Key Component in Investment Casting
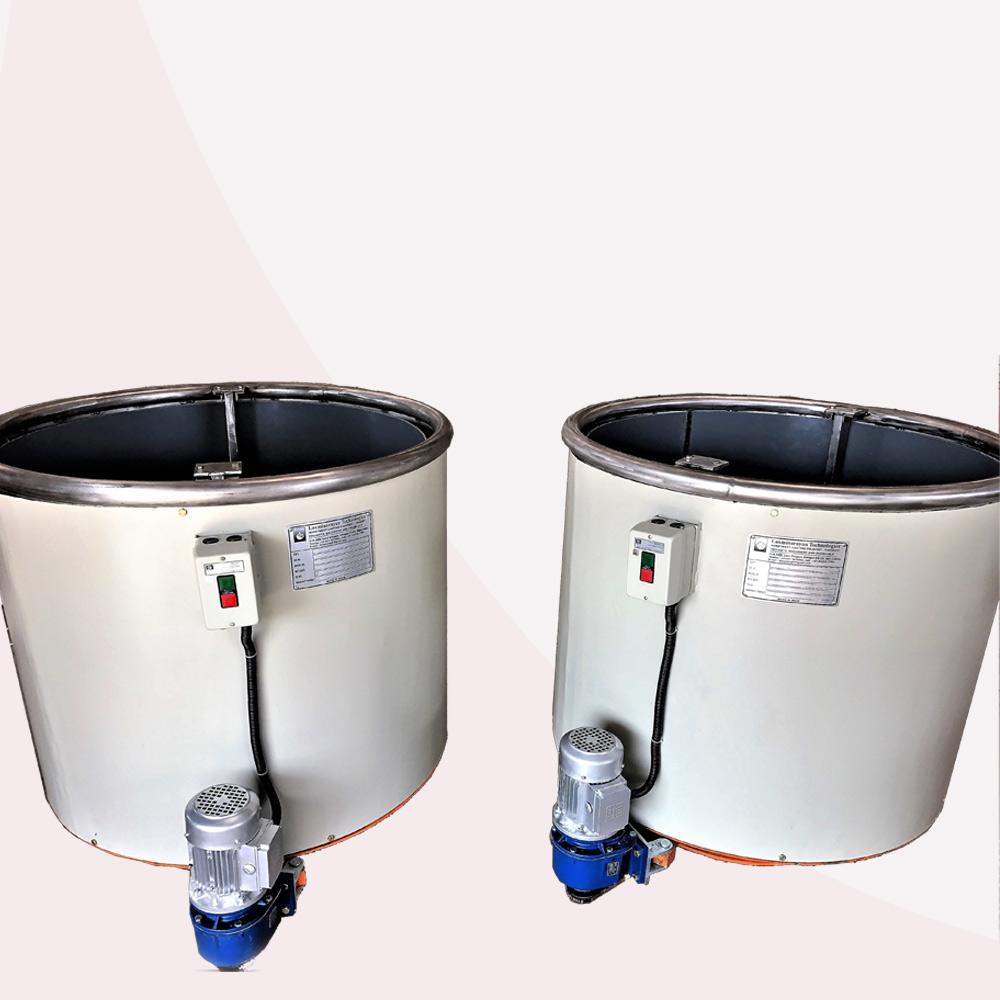
In the world of precision manufacturing, particularly within the investment casting industry, the slurry pot plays a vital role in ensuring high-quality castings. Also known as a dipping pot, cluster coating pot, or wax tree dipping pot, the slurry pot is an essential piece of equipment designed to facilitate the creation of ceramic molds used in investment casting. This article explores the functionality, features, and significance of the slurry pot, with insights drawn from industry leader Laxminarayan Technologies.
As detailed on their website https://www.ic-machines.com/slurry-pots/
What is a Slurry Pot?
A slurry pot is a specialized machine used in the investment casting process to hold and maintain a ceramic slurry—a mixture of refractory materials and binding agents—into which wax patterns or "trees" are dipped. This dipping process coats the wax patterns with a ceramic layer, which, once dried and hardened, forms a robust mold capable of withstanding the high temperatures of molten metal during casting. The slurry pot ensures that the slurry remains homogeneous and free from settling, which is critical for producing consistent, high-quality molds.
Key Features of the Slurry Pot
The slurry pot, as described by Laxminarayan Technologies, is designed with advanced engineering to meet the demanding needs of investment casting foundries. Here are its primary features:
-
Continuous Stirring Mechanism: The slurry pot is equipped with a vertical, rotating drum that works against a fixed baffle on the inner periphery of the tank. This continuous stirring action prevents heavier refractory materials in the slurry from settling or separating, ensuring a uniform mixture throughout the dipping process. This is crucial for maintaining the integrity of the ceramic coating.
-
Wall Wipers: To prevent slurry from adhering to the inner walls of the tank, the slurry pot includes wall wipers as a standard feature. These wipers keep the vessel clean, reducing material waste and ensuring consistent slurry quality.
-
Material and Design: The slurry pot is typically constructed from SS304 stainless steel, which provides durability and resistance to corrosion. Additionally, it features a removable polypropylene lining, which enhances ease of cleaning and maintenance while protecting the tank from wear.
-
Size Variability: Slurry pots are available in a range of diameters—600, 750, 1000, 1200, 1500, and 1800 mm—with appropriate drive systems to accommodate different production scales. This flexibility makes the machine suitable for both small and large foundries.
-
Maintenance-Free Operation: Designed for 24/7 operation, the slurry pot is engineered to be robust and low-maintenance, minimizing downtime and operational costs. This reliability is a hallmark of the machines produced by Laxminarayan Technologies, as highlighted in their promotional materials.
The Role of the Slurry Pot in Investment Casting
The investment casting process, often referred to as the "lost wax" process, involves creating precise metal components by forming a ceramic mold around a wax pattern. The slurry pot is integral to this process, as it enables the application of the ceramic slurry that forms the mold. Here’s how it fits into the workflow:
-
Slurry Preparation: The slurry, prepared in a primary or secondary slurry mixer, is transferred to the slurry pot using a slurry transfer pump. The slurry typically consists of refractory materials like aluminosilicates or fused quartz, combined with additives such as colloidal silica to maintain its properties.
-
Dipping Process: Wax trees—assemblies of wax patterns attached to a central sprue—are dipped into the slurry held in the pot. The continuous stirring ensures that the slurry coats the wax evenly, creating a uniform ceramic layer.
-
Stucco Application: After dipping, the coated wax trees are often sprinkled with stucco (a coarse refractory material) to enhance the mold’s strength. The slurry pot’s consistent slurry quality ensures that the initial coating adheres properly, setting the foundation for subsequent layers.
-
Mold Formation: Multiple layers of slurry and stucco are applied to the wax tree, building up a thick ceramic shell. Once complete, the wax is melted out (dewaxed), and the ceramic mold is fired to prepare it for metal pouring.
The slurry pot’s ability to maintain a consistent slurry composition is critical to producing defect-free molds, which directly impacts the quality of the final castings. This is particularly important for industries like aerospace, automotive, and medical, where precision components are essential.
Why Choose Laxminarayan Technologies’ Slurry Pot?
Laxminarayan Technologies, based in Kolhapur, India, is a renowned name in the investment casting machinery market, with a global presence in countries like Switzerland, Sweden, the USA, and Thailand. Their slurry pots are designed with a focus on quality, efficiency, and durability, offering several advantages:
-
Proven Design: The slurry pots are part of a comprehensive range of investment casting machinery, built with cutting-edge technology to ensure high productivity and low operating costs.
-
Global Reach and Support: With an established track record and worldwide installations, Laxminarayan Technologies provides reliable warranty and quick service response, ensuring minimal disruptions for foundries.
-
Customizable Solutions: The availability of multiple pot sizes and robust construction allows foundries to select a slurry pot tailored to their specific production needs.
-
Energy Efficiency: The company emphasizes energy-efficient designs, which contribute to lower operational costs and align with sustainable manufacturing practices.
Applications and Industry Impact
Slurry pots are indispensable in producing high-precision components for industries such as aerospace (e.g., jet engine parts), automotive (e.g., turbocharger components), and medical (e.g., implants). The consistent slurry quality provided by these machines ensures that the ceramic molds can withstand the rigors of high-temperature casting, resulting in components with excellent surface finish and dimensional accuracy.Moreover, the slurry pot’s role in maintaining slurry uniformity helps foundries achieve repeatability in their processes, reducing defects and improving yield. This is particularly valuable in high-stakes industries where even minor imperfections can lead to costly rework or product failures.
Conclusion
The slurry pot is a cornerstone of the investment casting process, enabling foundries to create precise, high-quality ceramic molds. With its advanced design features, such as continuous stirring, wall wipers, and durable construction, the slurry pot from Laxminarayan Technologies exemplifies reliability and efficiency. As detailed on their website https://www.ic-machines.com/, this machine is a testament to the company’s commitment to delivering world-class solutions for the precision casting industry. For foundries looking to enhance their production capabilities, the slurry pot is an investment in quality, consistency, and long-term performance.