Industrial Ovens Energy Efficiency: Cut Costs & Save Power
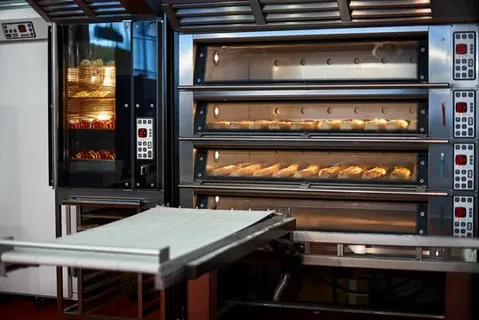
In today's competitive industrial landscape, energy efficiency has become a hot topic for manufacturers and bakers alike. With rising operational costs and increasing environmental awareness, businesses seek ways to optimize their processes without sacrificing quality. Industrial Ovens play a crucial role in this equation, as they are often significant energy consumers. But what if you could reduce your utility bills while boosting your production? By focusing on energy-efficient practices, you can achieve just that! Let’s explore some practical tips to enhance the performance of your Industrial-Ovens and minimize those pesky operational costs.
The Importance of Energy Efficiency in Industrial Baking and Manufacturing
Energy efficiency is crucial in industrial baking and manufacturing. It reduces operational costs and enhances productivity. By optimizing energy use, businesses can maximize their output while minimizing waste.
Reducing energy consumption contributes positively to the environment. Lower emissions mean a smaller carbon footprint, which aligns with global sustainability goals. This aspect becomes increasingly important as consumers favor eco-friendly practices.
Furthermore, investing in energy-efficient technologies boosts competitiveness. Companies that prioritize efficiency often enjoy improved profit margins and can allocate resources to innovation or expansion. Embracing energy-saving measures sets a foundation for long-term success in today's fast-paced market.
Common Energy Wastage Issues in Industrial-Ovens
Energy wastage in Industrial-Ovens can stem from several common issues. One major factor is poor insulation. If an oven isn't properly insulated, heat escapes quickly, leading to longer cooking times and higher energy bills.
Another significant issue is inefficient temperature control. Ovens run at inconsistent temperatures require more energy to maintain the desired heat level. This not only increases operational costs but can also affect product quality.
Improper oven loading contributes to energy waste. Overloading or unevenly distributing items prevents optimal airflow and results in longer cooking cycles. Addressing these concerns can lead to substantial savings while improving overall efficiency.
How Proper Insulation Improves Oven Efficiency
Proper insulation is crucial for enhancing the efficiency of Industrial-Ovens. High-quality insulation helps maintain consistent temperatures by minimizing heat loss and reducing energy consumption during operation. This stability not only improves product quality but also shortens cooking times.
When Industrial-Ovens are well-insulated, they require less energy to reach and sustain desired temperatures. This directly translates to lower operational costs and a smaller carbon footprint. As energy prices rise, efficient insulation becomes even more valuable.
Investing in advanced insulating materials can yield significant savings over time. These materials can withstand high temperatures while preventing thermal bridging and air leaks. The result is an oven that operates more efficiently, ensuring optimal performance throughout its lifespan.
The Role of Advanced Temperature Control Systems
Advanced temperature control systems are crucial in enhancing energy efficiency in Industrial-Ovens. These systems allow for precise heat regulation, ensuring that the required temperatures are maintained consistently throughout the baking or manufacturing process. This precision reduces unnecessary energy consumption since the oven does not have to overcompensate for fluctuations.
Innovative technologies such as predictive analytics and real-time monitoring can significantly enhance performance. By using sensors and IoT (Internet of Things) devices, manufacturers can track temperature levels and adjust them automatically based on production needs. This responsiveness minimizes energy waste and optimizes operational efficiency.
Investing in cutting-edge temperature control technology is not just about immediate savings; it's also about future-proofing operations against rising energy costs. As industries move towards more sustainable practices, having efficient equipment will become increasingly important. Ultimately, implementing advanced temperature control systems is a smart strategy that enhances productivity while reducing costs associated with energy inefficiencies in Industrial-Ovens.
Choosing the Right Fuel Source for Cost-Effective Operation
Selecting the appropriate fuel source for Industrial-Ovens is a critical decision that directly impacts energy efficiency and operational costs. The right choice can lead to significant savings, reduced environmental impact, and improved performance. Here are key considerations to help you make an informed decision.
Understanding Fuel Types and Their Efficiency
Different fuel types, such as natural gas, electricity, propane, and oil, have varying energy efficiencies and costs. Natural gas is often preferred for its cost-effectiveness and lower emissions, while electricity offers precise temperature control but can be more expensive. Propane and oil are alternatives but may require additional storage and handling. Evaluating the efficiency of each fuel type and your oven’s requirements is essential.
Analyzing Fuel Availability and Costs
The availability and cost of fuel sources vary by region. Natural gas might be economical in areas with abundant supply, whereas electricity could be more viable in regions with renewable energy incentives. Conduct a thorough analysis of local fuel prices and availability to determine the most cost-effective option for your operations.
Evaluating Environmental Impact
Sustainability is a growing concern in industrial operations. Natural gas and electricity from renewable sources have a lower carbon footprint than oil or propane. Choosing a fuel source with minimal environmental impact reduces operational costs and aligns with eco-friendly practices.
Considering Oven Design and Compatibility
Not all ovens are compatible with every fuel type. Your oven's design and heating mechanisms must align with the chosen fuel source. For instance, electric ovens are ideal for processes requiring precise temperature control, while gas ovens are better suited for high-temperature applications. Ensure compatibility to maximize efficiency.
Long-Term Cost and Maintenance Implications
Beyond initial costs, consider long-term expenses such as maintenance, fuel storage, and potential price fluctuations. Electric ovens may have lower maintenance costs, while gas ovens require regular inspections. Weigh these factors to make a sustainable and cost-effective choice for your industrial oven operations.
Regular Maintenance Practices to Enhance Energy Efficiency
Regular maintenance is key to keeping Industrial-Ovens running efficiently. Scheduling routine checks can help identify any wear and tear that may lead to energy loss. Simple practices like cleaning the oven's interior, checking for leaks, and ensuring proper sealing can make a significant difference.
Monitoring temperature sensors is also crucial. Over time, these devices can become inaccurate, leading to overheating or underheating. Recalibrating them ensures your oven operates within optimal ranges, reducing unnecessary energy consumption.
Don’t overlook the importance of inspecting insulation materials as well. Damaged or degraded insulation allows heat to escape, forcing the oven to work harder than needed. Addressing such issues promptly will enhance performance while lowering operational costs.
The Impact of Load Optimization on Energy Consumption
Load optimization plays a crucial role in enhancing energy efficiency in Industrial-Ovens. By ensuring that the stove is loaded to its optimal capacity, manufacturers can maximize heat distribution and minimize waste. This approach leads to more consistent cooking or baking results.
When an oven operates with uneven loads, it may require additional energy to maintain temperature levels. This inefficiency raises operational costs and increases wear on equipment over time. Balancing load helps mitigate these issues and extends the lifespan of Industrial-Ovens.
Moreover, effective load management can lead to faster processing times. With proper scheduling and organization, businesses can achieve higher output while reducing energy consumption—making load optimization a smart strategy for sustainable manufacturing practices.
Upgrading to Modern High-Efficiency Industrial Ovens
Upgrading to modern, high-efficiency Industrial Ovens can significantly impact your energy costs. These new models are designed with advanced technology that optimizes heat distribution and reduces energy consumption. This means lower utility bills and a smaller carbon footprint.
Many of these high-efficiency units incorporate features like variable speed fans and improved insulation, leading to faster cooking times and better product quality. Less time in the oven translates to higher productivity for your operation.
Investing in modern ovens can also enhance safety standards. With better temperature control systems, you reduce the risk of overheating or undercooking products, ensuring consistent results every time. Making this upgrade offers numerous operational advantages that go beyond just energy savings.
Government Incentives and Rebates for Energy-Efficient Equipment
Governments worldwide recognize the importance of energy efficiency, particularly in industrial settings. Many offer incentives and rebates to encourage businesses to invest in energy-efficient equipment. These programs can significantly reduce initial costs for upgrading ovens, making it easier for companies to transition to more sustainable operations.
For instance, tax credits may be available for businesses that adopt high-efficiency appliances or systems. Grants are another option, providing financial assistance to improve energy performance within manufacturing processes. Moreover, utility companies often run their incentive programs. They might offer cash rebates or discounts on electricity rates when businesses m
Staying informed about these opportunities is essential for maximizing cost savings while enhancing operational efficiency. Engaging with local government representatives and industry associations can help identify which incentives apply directly to your situation. By leveraging these resources, industries contribute positively to the environment and boost their bottom line through reduced operational costs over time.
Implementing Heat Recovery Systems for Waste Reduction
Heat recovery systems are an effective strategy for reducing waste in industrial-ovens. These systems significantly improve energy efficiency by capturing and reusing heat generated during the baking or manufacturing process. Instead of letting valuable thermal energy escape, businesses can redirect it to preheat incoming air or materials.
Implementing such a system lowers operational costs and contributes to sustainability goals. Industries can reduce their carbon footprint by minimizing reliance on additional fuel sources for heating needs.
Moreover, heat recovery enhances overall productivity. With more consistent temperatures and reduced energy demands, ovens operate more efficiently, improving product quality and lowering emissions over time. This is a win-win situation for both profitability and environmental responsibility.
Conclusion
Energy efficiency in Industrial Ovens is not just a trend; it's a necessity for sustainable operations. Businesses can significantly cut costs while minimizing their environmental footprint through various strategies. Investing in modern technologies and proper maintenance can lead to remarkable savings. From advanced temperature controls to heat recovery systems, each improvement adds up. As manufacturers strive for excellence, embracing energy-efficient practices will enhance productivity. The future of industrial baking and manufacturing hinges on these smart choices that benefit both the bottom line and the planet.
FAQs
Energy efficiency in Industrial-Ovens is vital to operational sustainability and cost management. By focusing on various strategies—ranging from proper insulation to advanced temperature control systems—businesses can significantly reduce energy wastage while also enhancing their baking or manufacturing processes.
What are the main benefits of improving energy efficiency in Industrial Ovens?
Improving energy efficiency of Industrial Ovens leads to lower operational costs, reduced carbon footprint, and a longer lifespan for your equipment.
How often should I perform maintenance on my industrial oven?
Regular maintenance is crucial. It’s generally recommended that you inspect your ovens at least once every six months, but this may vary depending on usage intensity.
What types of fuel sources are most cost-effective for operating Industrial-Ovens?
Natural gas is one of the most economical fuel sources due to its availability and relatively low price. However, it’s also essential to analyze local market conditions.
Grading my oven leads to significant savings?
Yes. Modern high-efficiency Industrial-Ovens often use less energy than older models, leading to substantial long-term savings.
Are there government incentives available for implementing energy-efficient technologies?
Many governments offer rebates and tax incentives for businesses that invest in energy-efficient equipment. Checking with local regulations can help you find applicable programs.
Related Business Listings |