The Durable Beauty of Composite Shiplap for Outdoor Spaces
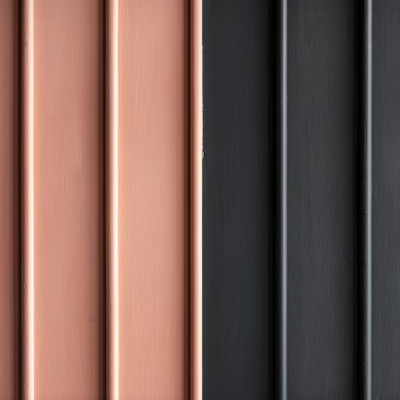
Introduction
Designing the perfect outdoor space involves choosing materials that not only look great but also stand the test of time. Composite shiplap is increasingly being used in patios, garden walls, and outdoor kitchens because it delivers on both fronts. Let’s explore why this material is a game-changer for exteriors.
Composite Shiplap: Built to Withstand the Elements
Outdoor environments demand more from building materials. With rain, sun, and temperature fluctuations, wood often fails to maintain its integrity. That’s where composite shiplap comes in. Its weather-resistant composition ensures it won't warp, crack, or fade easily—even after years of exposure.
Stylish and Sustainable Outdoor Wall Paneling
Besides its strength, composite shiplap also offers incredible design potential. Whether you want a sleek urban look or a cozy cabin feel, it’s easy to find a product that matches your aesthetic.
And it's not just beautiful—it’s environmentally friendly too. Many composite shiplap products are made using recycled materials, offering sustainability without sacrificing style.
Conclusion
Upgrade your backyard or porch with the elegant durability of composite shiplap. As experts in wall paneling, we’ve seen how this material performs in all weather and across all designs. Strong, stylish, and sustainable—composite shiplap is the perfect outdoor solution.