Workplace Hazards A Guide to Managing Risks and Ensuring Safety
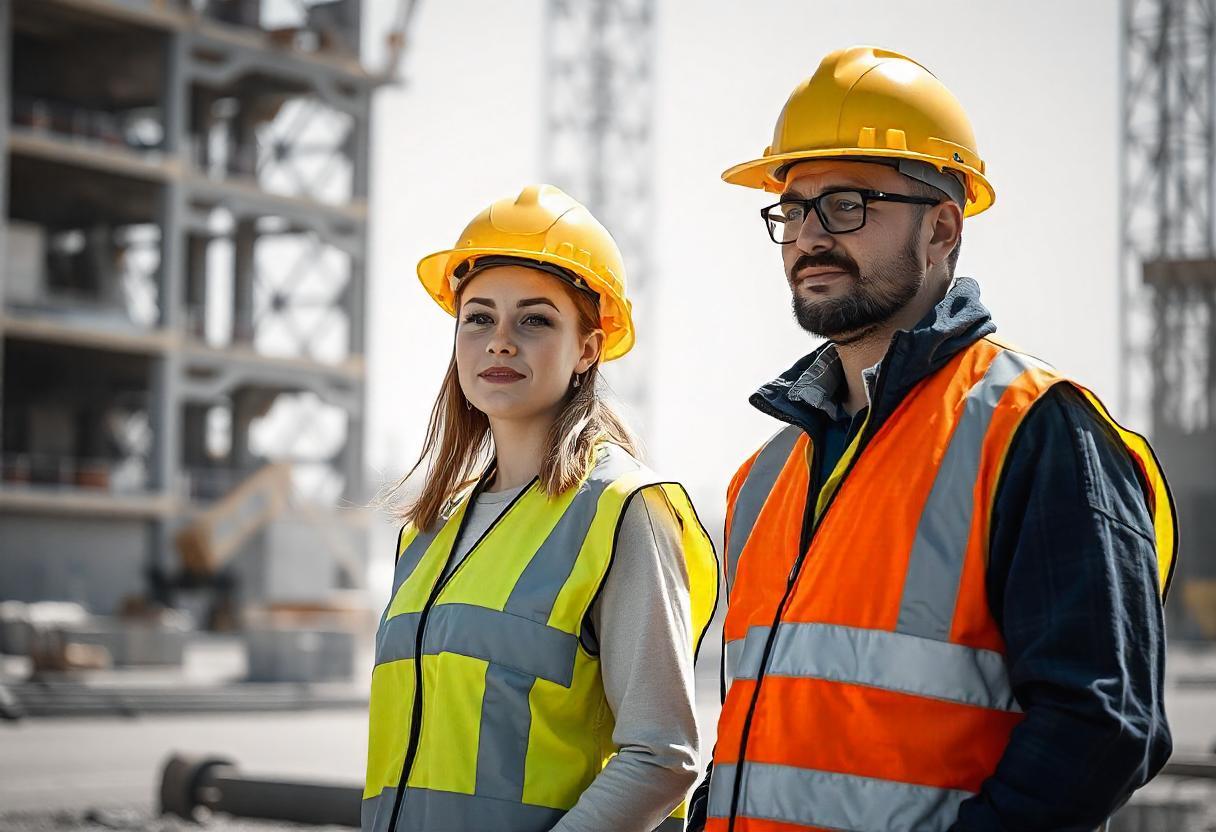
Workplace hazards can be present in many forms—whether it's heavy machinery, chemicals, or even everyday tasks like lifting boxes. No matter the type of hazard, if not managed properly, they can lead to serious injuries. This is where workplace safety management comes into play. Businesses need to invest in comprehensive safety training, equipment, and practices to protect their employees from potential harm.
Enrolling in a NEBOSH IGC (International General Certificate) can provide essential knowledge for identifying and managing these hazards effectively. In this article, we'll explore some key workplace hazards, real-life examples, and steps businesses can take to reduce the risks. Let’s dive into some real case studies and a practical step-by-step guide.
The Impact of Manual Handling Hazards
In many workplaces, especially in warehouses, construction sites, and retail, manual handling is a daily activity. Unfortunately, this task, when done incorrectly, can lead to severe injuries. When employees handle loads that are heavy, awkward, or out of reach, the risks of back pain, strains, and falls increase significantly. These types of hazards are commonly referred to as manual handling hazards, and they often go unnoticed until an injury occurs.
Real-Life Example: John’s Injury at a Warehouse
John worked in a warehouse, regularly lifting heavy boxes from high shelves. His job required him to stretch beyond his natural reach to lift these loads. One day, after performing the same task hundreds of times without the proper safety measures, he twisted his back awkwardly while reaching for a heavy box. Unfortunately, this caused a slipped disc that led to months of painful recovery and physical therapy.
Employers often overlook these seemingly routine tasks, but they can be hazardous if proper precautions are not taken. This is why training in safe manual handling practices is essential for all workers.
The Hidden Risks of Poor Manual Handling
Manual handling hazards can result in several long-term health problems, including:
-
Back and Muscular Injuries: Lifting heavy objects, especially from awkward positions, places undue strain on the spine and muscles.
-
Increased Risk of Falling Objects: When lifting out-of-reach loads, the chances of accidentally dropping something increase, leading to injuries like broken toes or head trauma.
-
Poor Posture Leading to Chronic Issues: Repetitive motions and poor posture during lifting can cause long-term joint and muscle damage.
Real-Life Example: Lisa’s Neck Injury
Lisa worked as a retail stocker in a store. She frequently leaned forward to grab boxes from the top shelves, straining her neck and shoulders over time. After several years of this improper lifting technique, Lisa developed severe neck pain that required surgery. It could have been avoided if her employer had introduced proper safety measures, such as lifting aids and safer work practices.
How to Prevent Manual Handling Hazards
Step 1: Provide Proper Training
Training employees in safe lifting and handling techniques is one of the most effective ways to reduce risks. Proper posture, lifting techniques, and awareness of physical limits can make a huge difference. Safety training courses, such as those offered in Safety Officer Course in Pakistan, provide employees with knowledge on how to handle these tasks without endangering their health.
Step 2: Use Mechanical Aids
Instead of relying on employees to manually lift heavy objects, employers should provide mechanical aids such as:
-
Step ladders or safety stools for reaching high shelves
-
Lifting trolleys or forklifts for transporting heavy loads
-
Hoists or vacuum lifters for bulky or awkward items
Step 3: Redesign Workspaces
Employers should take steps to reduce the need for manual lifting altogether. For example, arranging shelves at waist height, using adjustable workstations, or automating repetitive lifting tasks can drastically minimize the risks.
Step 4: Implement Personal Protective Equipment (PPE)
PPE plays a critical role in preventing injuries. Workers should wear gloves to maintain a good grip, back support belts for added stability, and steel-toe boots to protect themselves from dropped objects.
For those who want to gain an in-depth understanding of workplace safety and how to handle these hazards effectively, investing in a Safety Officer Course in Multan is a good choice.
Read More: Safety Officer Course in Multan
The Role of Safety Officer Courses in Preventing Workplace Hazards
A Safety Officer Course is designed to equip individuals with the necessary skills and knowledge to identify, assess, and control workplace hazards. These courses provide essential training in areas such as risk assessments, emergency procedures, and legal requirements, making them a vital investment for any company looking to ensure employee safety.
Why Investing in Safety Officer Courses is a Smart Choice
Investing in a Safety Officer Course isn’t just about compliance—it’s about protecting your employees and ensuring that your workplace is safe. By having certified safety officers on-site, businesses can prevent accidents, reduce workplace injuries, and create a culture of safety.
Moreover, these courses help in understanding the legal obligations that employers have to meet regarding workplace safety. For example, in Pakistan, the Safety Officer Course in Pakistan is recognized for training individuals to oversee safety regulations effectively, reducing risks for both employees and employers.
Step 5: Regularly Assess and Update Safety Procedures
Employers must continuously assess the effectiveness of their safety protocols. Conduct regular safety audits and keep up to date with any new safety standards or legal requirements. Encouraging feedback from employees about potential hazards they encounter on the job can also be invaluable in creating safer work environments.
Real-Life Example: A Manufacturing Plant’s Transformation
One manufacturing plant in Pakistan struggled with frequent injuries due to improper lifting techniques and inadequate safety measures. After sending their employees for training in a Safety Officer Course in Pakistan, the company revamped their safety protocols. They introduced new lifting aids, conducted regular safety drills, and provided ongoing training. Within a year, the number of workplace injuries dropped by 40%, proving that investing in safety is well worth it.
How Safety Training Can Boost Employee Confidence
Safety training doesn’t just reduce risks—it also boosts employee confidence. When employees know they have the knowledge and tools to safely perform their tasks, they feel more confident in their roles. This increased confidence can lead to greater productivity, fewer accidents, and a more positive work environment.
Real-Life Example: Sarah’s Confidence After Safety Training
Sarah, a warehouse worker, was initially afraid to use the forklifts because she wasn’t sure of the safety protocols. After completing a Safety Officer Course in Multan, she gained the skills and knowledge she needed to operate the equipment confidently. As a result, not only did her performance improve, but she also felt empowered to contribute suggestions to improve safety in the warehouse.
The Value of Ongoing Safety Courses for Employers and Employees
The workplace is constantly evolving, and so are the hazards. That’s why employers must prioritize ongoing safety training to ensure their teams stay up-to-date with the latest safety protocols and regulations. Investing in courses like Safety Officer Course in Pakistan and other relevant safety programs helps businesses stay compliant and, more importantly, keeps employees safe.
In conclusion, workplace hazards are a significant concern for employers, but by investing in comprehensive safety training, proper equipment, and proactive safety measures, businesses can drastically reduce the risk of injuries. Whether it’s improving manual handling practices or enrolling in a Safety Officer Course in Pakistan, safety should always be a top priority for businesses looking to protect their most valuable asset—employees.
Read More: Safety Officer Course in Multan
Final Thoughts
When it comes to handling workplace hazards, it’s better to be proactive than reactive. A Safety Officer Course is an essential step in creating a safer workplace. From manual handling risks to hazardous machinery, there are plenty of areas to focus on, but with the right training and protocols in place, businesses can ensure a safer, more productive environment for their employees.
If your company is committed to improving safety, investing in safety training is the first step toward making real changes. How does your company ensure workplace safety? Share your insights below!