Categorii
Citeste mai mult
When it comes to maintaining or improving the appearance of your home, one of the most effective ways to enhance its curb appeal is through painting. House painters, professionals who specialize in residential painting services, play a crucial role in transforming the aesthetic of homes. Whether you’re looking to refresh the interior, give the exterior a new look, or protect...
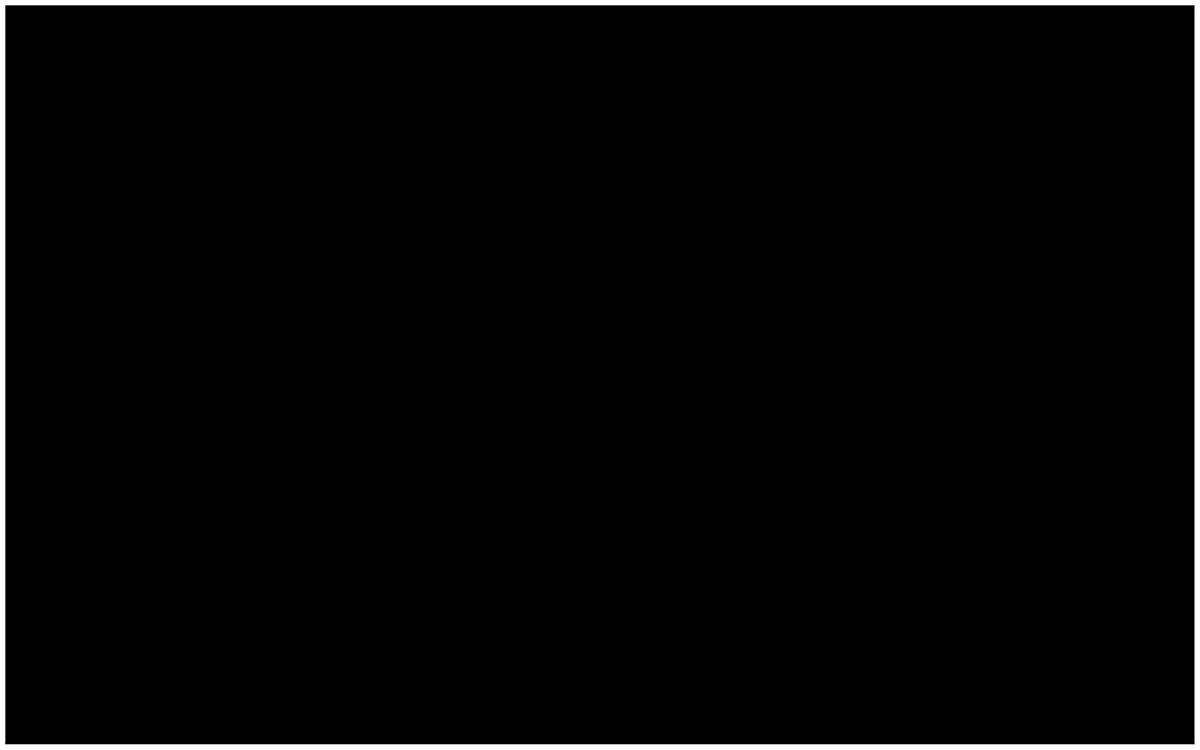
The Silicon Based Paper Market sector is undergoing rapid transformation, with significant growth and innovations expected by 2028. In-depth market research offers a thorough analysis of market size, share, and emerging trends, providing essential insights into its expansion potential. The report explores market segmentation and definitions, emphasizing key components and growth...
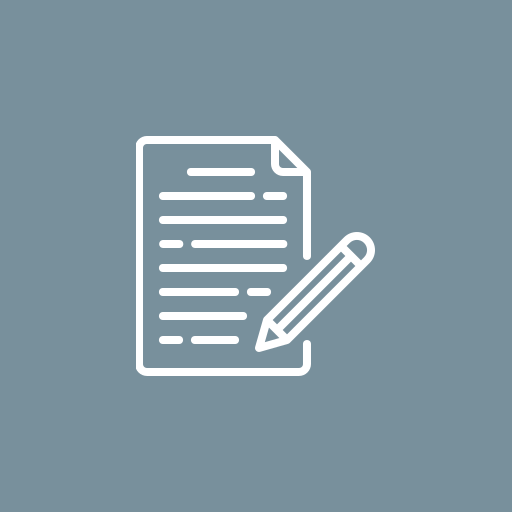
Keloids are raised, thickened scars that form when the body’s natural healing process goes into overdrive, producing excessive amounts of collagen. While they are not dangerous, keloids can cause discomfort, itching, tightness, and cosmetic concerns—especially when they develop on visible parts of the body like the chest, shoulders, or jawline. If you've experienced keloids before,...
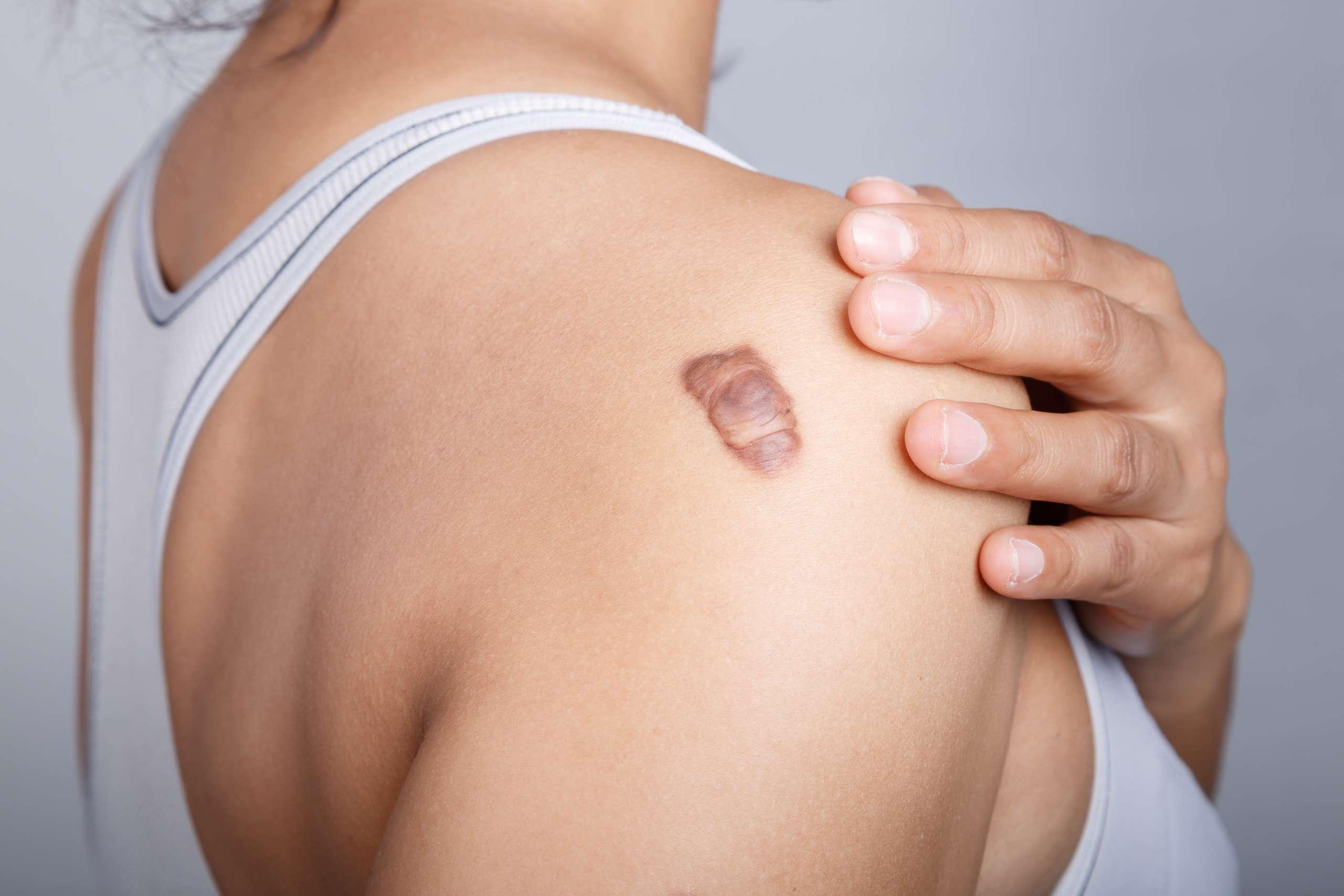
Kyrgyzstan, a paradise of unspoiled nature and the ancient culture, is rarely visited by those who look for the beaten tracks. Kyrgyzstan has much untapped landscapes that range from high peaks of mighty mountain ranges to quiet lakes. For those who love off the beaten track destinations, the Kyrgyzstan Tour is the ideal way to explore the country’s hidden treasure and enjoy the raw...
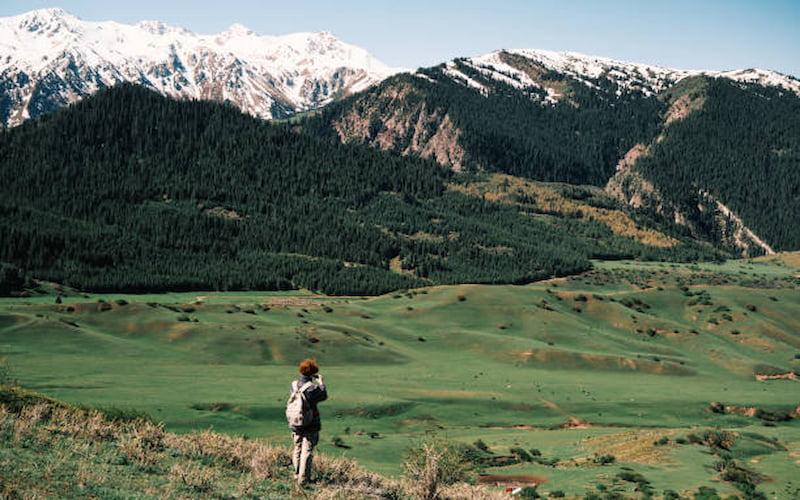
For individuals seeking a reliable and private way to monitor their blood alcohol concentration (BAC), a home blood alcohol test is an essential tool. Esspron offers user-friendly, certified blood alcohol testing kits that provide accurate readings from the comfort of your home. Whether you're tracking sobriety, preparing for a legal requirement, or just ensuring you're safe to drive,...
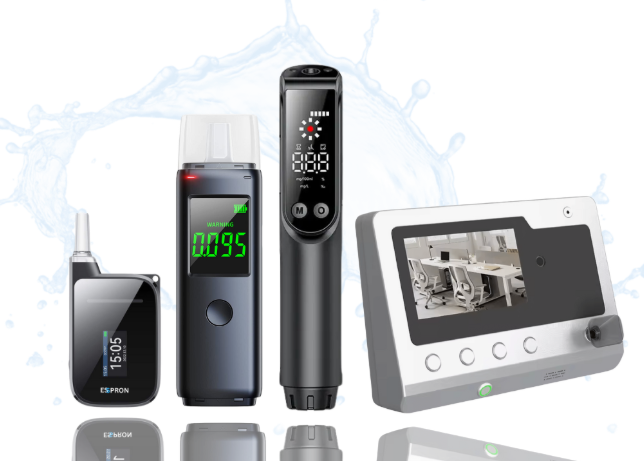