Categorie
Leggi tutto
The moment you resolve to partner with Green-Leap Skips, you choose not a mere skip company but rather an Eco-wary top skip hire service in Cardiff that has an exceptional 90% recycling rate. In contrast to the mainstream skip hire companies that dump their waste in landfills, we have developed an advanced sorting system that revamps, recycles or recovers energy from nearly all the waste...
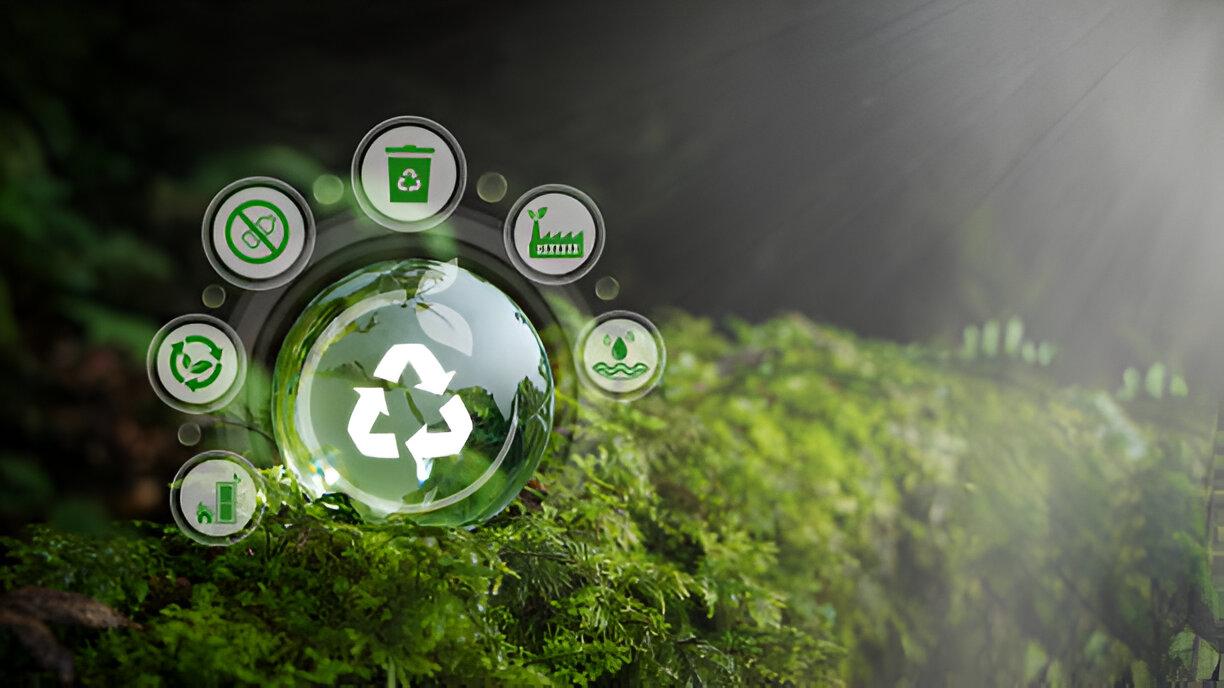
هل سئمتِ من غسل الصحون بعد كل وجبة؟ الكترو هوم يقدّم لكِ الحل الذكي والمريح! مع أقوى عروض غسالات الصحون، أصبح بإمكانكِ التخلّي عن عناء التنظيف اليومي والاستمتاع براحة تستحقينها دون المساس بنظافة مطبخكِ. لماذا تشتري غسالة صحون من الكترو هوم؟ 🔹 تنوع كبير في الأنواع والموديلات لتناسب كل مطبخ 🔹 أسعار مميزة وتخفيضات مستمرة على مدار العام 🔹 ماركات عالمية موثوقة بأحدث التقنيات 🔹...
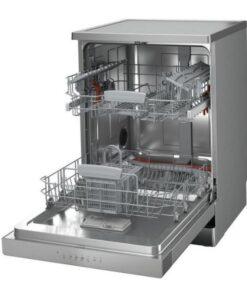
Global 2-Hydroxyethyl Methacrylate (HEMA) market demonstrates steady growth, valued at USD 517 million in 2024 and projected to reach USD 657 million by 2032, expanding at a CAGR of 3.6%. This growth is primarily driven by its extensive applications in coatings, adhesives, and reactive resins, alongside increasing demand from end-use industries prioritizing...
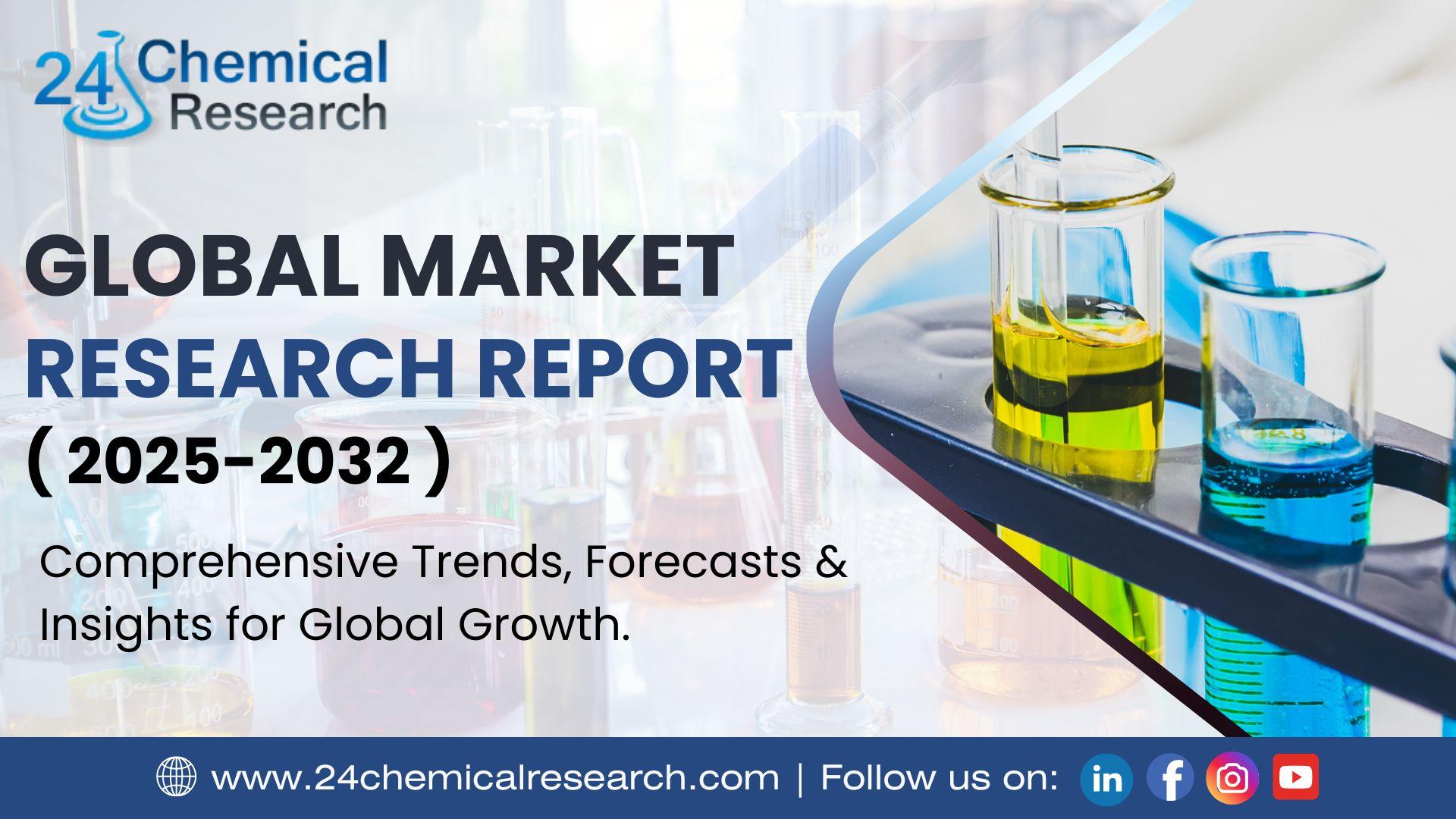
Introduction: The development of technology in the current digital environment has given rise to many connectivity possibilities. USB (Universal Serial Bus) became known as the standard for data transfer and charging among the various ports available. With an increasing use of advanced technologies, USB-C is swiftly becoming the current standard for many devices, including...
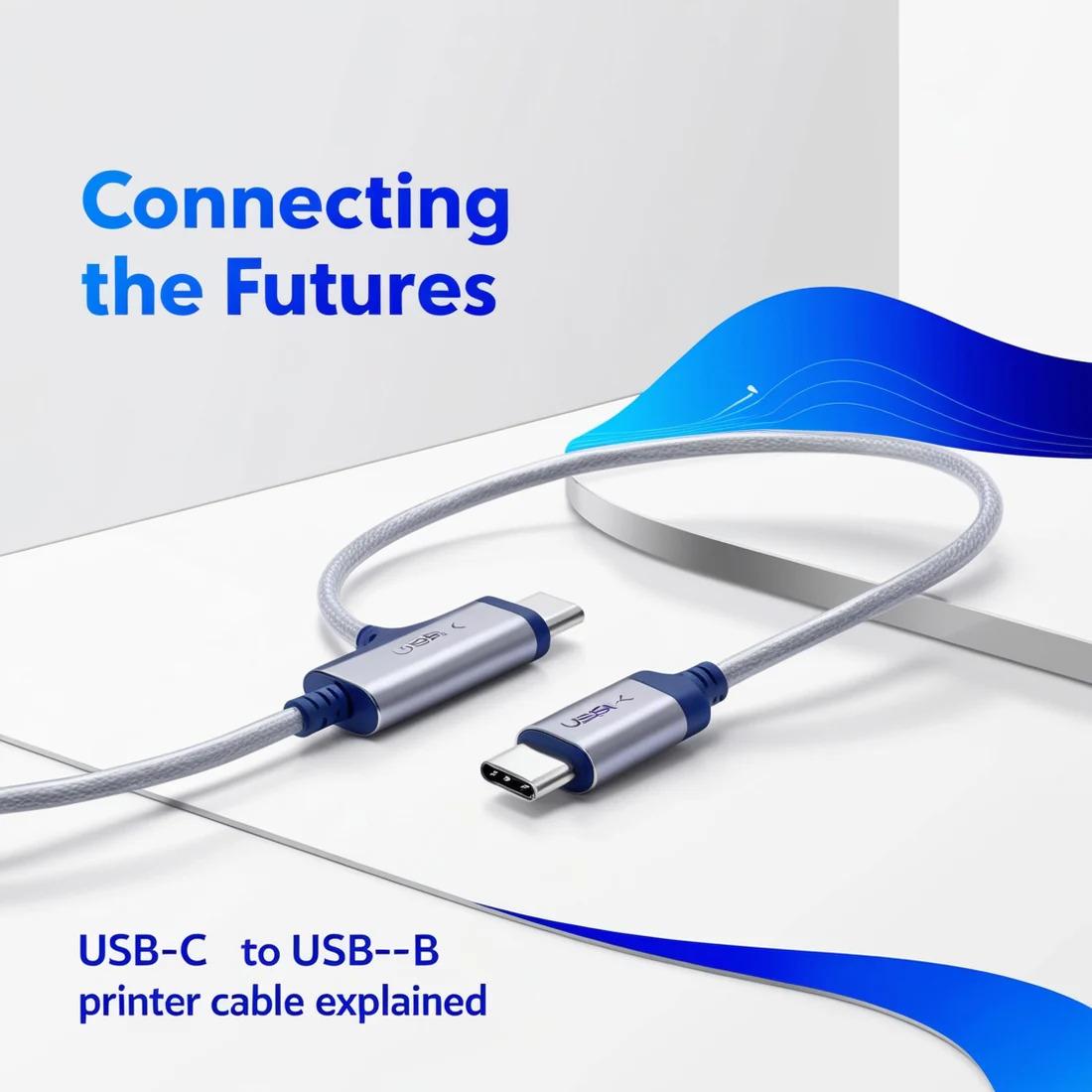
The Public Transport Market sector is undergoing rapid transformation, with significant growth and innovations expected by 2029. In-depth market research offers a thorough analysis of market size, share, and emerging trends, providing essential insights into its expansion potential. The report explores market segmentation and definitions, emphasizing key components and growth drivers....
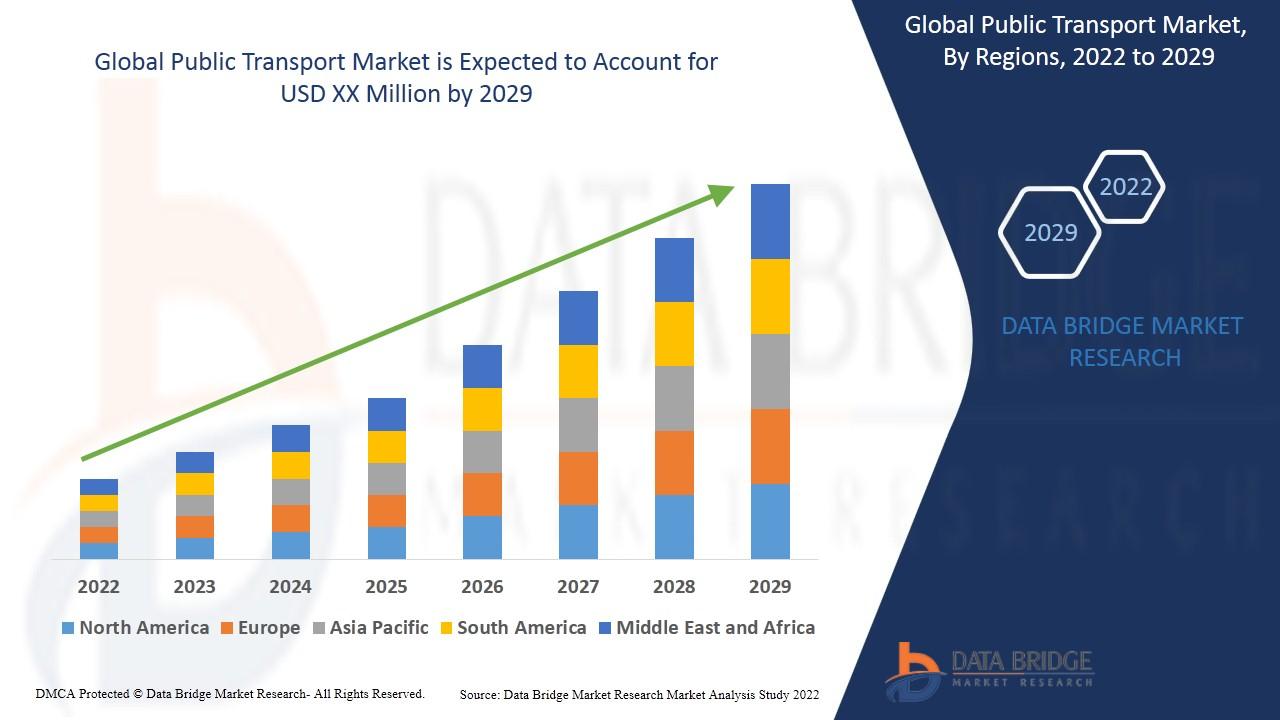